What’s that smell? (And other questions about the future of work)
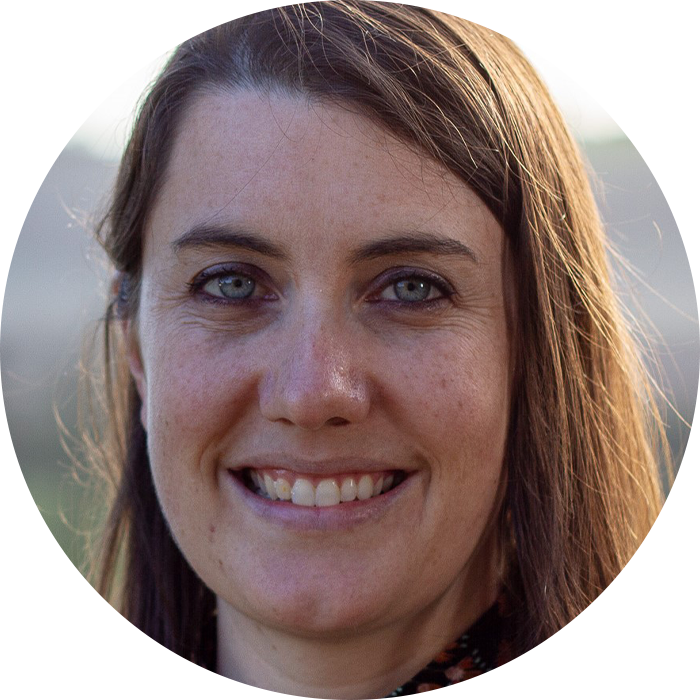
It’s estimated that 800,000 manufacturing jobs are unfilled in the US alone, and experts say that the gap could rise to 2.1M by 2030. The manufacturing industry is also grappling with its emissions and waste footprint – and the irreversible effects of climate change we are already seeing as a result.
The imperative to change how we make things has never been greater.
Last week, as part of #tedcountdown I had the privilege of leading a Quest to see firsthand the future of manufacturing in Detroit with LIFT and Siemens. It was an immersive masterclass in change management and leadership at the intersection of people and technology.
Here’s what I learned:
A stronger workforce starts with inclusive skills development
Walking through Detroit’s oldest surviving neighborhood, a juxtaposition of trendy new developments and long abandoned properties, you might be surprised to stumble upon $50 million of leading edge manufacturing research and development equipment.
In Corktown, Detroit public-private partnership LIFT operates a 100,000 square foot facility where they are shaping new ways to accelerate technology, develop talent and convene collaborators in service of smarter manufacturing.
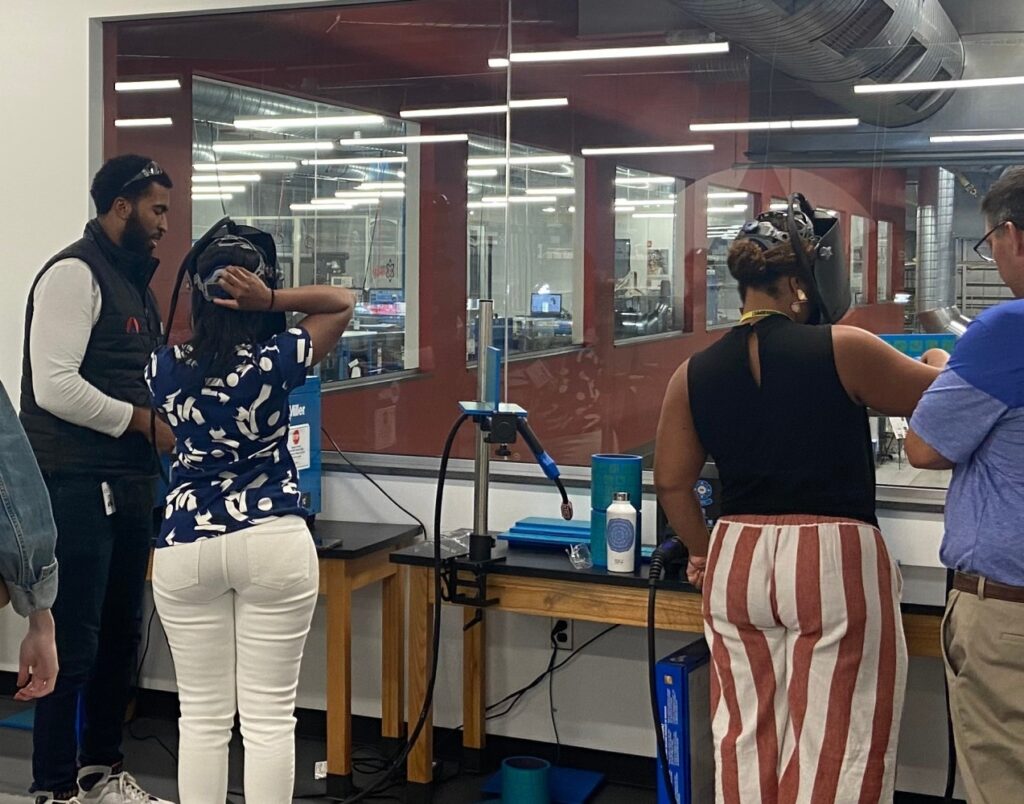
Our Quest began with a visit to LIFT’s Learning Lab, a place for local high school students to gain immersive training and certification in high-demand manufacturing skills, such as robotics. They let us try out virtual welding (much harder than it looks!) — which uses VR to teach and practice welding skills and is one of many tracks offered to gain career credentials. LIFT also hosts Operation Next, a program supporting military personnel to transition into manufacturing careers. One veteran spoke candidly with us about the challenge of building a civilian career after 20 years of active duty, emphasizing the importance not just of building skills but also being given chances to apply them.
LIFT creates career opportunities but it’s up to industry to give chances to a new, highly trained workforce by expanding hiring practices.
The Industrial Metaverse and Digital Twins are the tech you didn’t know you need to know about
We then moved to a vast production floor to see how Siemens, a leading global technology company focused on industry, infrastructure, transport, and healthcare and one of LIFT’s industry partners, is applying emerging technologies to develop and commercialize products more sustainably, and faster. Drew Whitney showed us how the Industrial Metaverse (or IMV for those in the know) and Digital Twins allow engineers to build and test in the virtual world before any production begins. Imagine testing a car in all kinds of weather conditions but without…the car. They do that here. The reduction of waste — in materials, byproducts, and time — opens up a world of possibilities for the entire manufacturing sector, and offers a path to drastically reduce emissions from manufacturing.
The Industrial Metaverse is critical to building a more sustainable future – and we need more passionate people who know how to work in it.
Software and robots are not replacing us (just one example)
While technology can do more and more (including teaching itself), people are driving tech’s use. Drew and his team, including mentors who have decades of experience in industry, showed us how expertise is being passed down not just through word of mouth but meticulous documentation in tech systems, supplemented by AI which updates learnings at scale.
Highly skilled work requires mentorship and apprenticeship. New tech is enhancing, not replacing these activities.
This work takes a whole lotta love
We rounded out the day in conversation with Christine Longroy, Senior Director of Ecosystem at LIFT and Barbara Humpton, CEO of Siemens USA… which brings me back to my title: what’s that smell?
The smell of the production floor is almost an absence of smell — fresh, not sterile, and too subtle to be familiar. Only half jokingly, a participant asked what gave the floor its ‘I can’t put my finger on it’ scent. Likely, it’s simply the result of a clean space and clean production processes. But some of our participants observed the beauty of the production floor, describing what they saw as processes that mimicked nature — so maybe new American industry looks and smells a lot more like the natural world than we’d expect.
Of course, the questions for Christine and Barbara went much deeper. We discussed the complexity of managing a vast global value chain, the importance of glocalization and frameworks for decision making, and how investment in communities accelerates innovation. Knowing stakeholders where they live and work, knowing what you value as an organization, and learning from experience are essential.
We need more leaders like Barbara and Christine, who despite the challenges of the world see possibility and hope, who believe in people and innovation, who create opportunities and inspire others to do the same.
(On that note, I highly recommend listening to Barbara’s podcast, The Optimistic Outlook.)
Conclusion
On the surface, this Quest visit was about infrastructure and technology – but it ended up really being about love, abundance, and optimism. A fun example: At one point, Cathe Reams, Siemens’ Communications Director, generously shared the shoes off her feet so a participant could explore the production floor (talk about walking the talk!).
To anyone serious about change, I leave you with this: You have to see it to understand it. You have to meet the people driving it and ask good questions to adapt yourself. And you have to put people in the center to solve the challenges we collectively face — in industry and beyond.
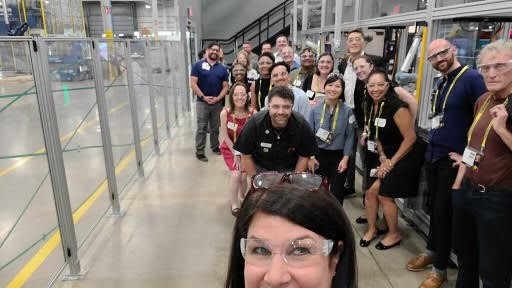
I’m grateful to LIFT and Siemens for inviting us to step into their world, the future. I hope their work inspires you too.